A Comprehensive Guide to Industrial Surface Preparation Techniques
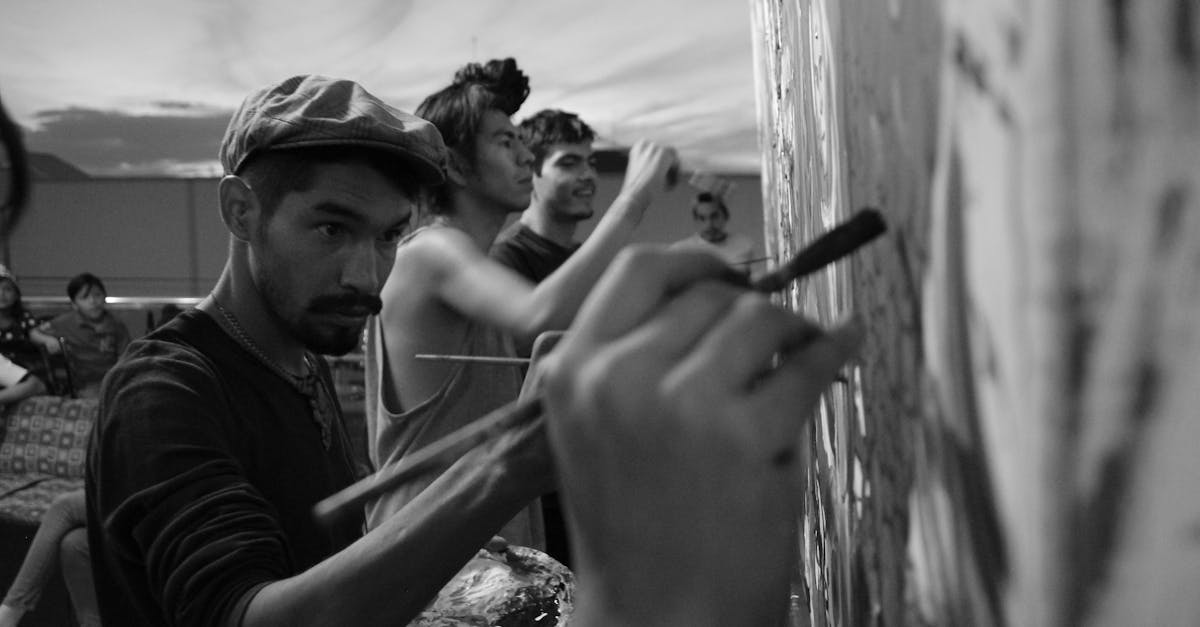
Table Of Contents
The Use of Waterjet Cutting
Waterjet cutting employs high-pressure streams of water to cut through various materials, making it a versatile technique across multiple industries. This method is particularly effective for cutting metals, plastics, glass, and even ceramics. Operators can customise waterjet systems with abrasive materials to enhance cutting efficiency, allowing for precise and intricate designs. The versatility of waterjet cutting makes it suitable for both thick and thin materials, offering flexibility in application.
The precision of waterjet technology reduces the need for secondary processing, thereby streamlining the manufacturing workflow. Waterjet cutting generates minimal thermal distortion, which preserves the integrity of the material. This capability is crucial in applications where maintaining dimensions is paramount. Overall, waterjet cutting stands out for its ability to deliver detailed results while being less harmful to the environment compared to traditional cutting methods that may involve more harmful substances or produce hazardous waste.
Benefits of High-Pressure Water in Surface Cleaning
High-pressure water systems have become integral in modern surface cleaning processes due to their effectiveness and efficiency. The use of water at elevated pressures can easily remove dirt, grease, and contaminants from surfaces without damaging the underlying material. This method is particularly beneficial for sensitive substrates where traditional cleaning techniques, such as abrasive blasting, may cause significant harm.
Moreover, high-pressure water cleaning is an eco-friendly alternative to chemical-based methods. It eliminates the need for harmful solvents and reduces the environmental footprint associated with hazardous waste disposal. The process generates minimal waste, relying mainly on recycled water, which promotes sustainability in industrial practices.
Surface Profiling Methods
Various techniques are employed to achieve precise surface profiling essential for optimal coating adhesion. Abrasive blasting is one of the most common methods, leveraging materials such as sand or walnut shells to create a roughened surface. This technique effectively removes contaminants while inducing a surface texture that enhances mechanical adhesion. Another method is mechanical grinding, which utilises grinding wheels to achieve a specific roughness based on the required coating specifications. This approach is beneficial for preparing surfaces of various geometries and materials, ensuring uniformity and consistency.
In addition to traditional methods, advancements in technology have introduced non-destructive techniques like laser scanning and ultrasonic testing. These approaches allow for precise measurement and assessment of surface profiles without compromising the integrity of the material. By combining these modern techniques with conventional profiling methods, industries can ensure that surfaces meet required standards for finishing. Properly profiling surfaces not only supports better adhesion of coatings but also contributes to the longevity and performance of the finished product.
Measuring Surface Roughness for Coating Adhesion
Surface roughness plays a critical role in determining how well coatings adhere to a substrate. It is essential to achieve a specific texture that enhances mechanical interlocking between the coating and the surface. Various methods exist for measuring roughness, including profilometry, which utilises a stylus to trace the surface profile. Alternatively, optical methods provide non-contact measurements, ensuring that delicate surfaces remain unscathed during evaluation. Understanding the roughness parameters such as Ra (average roughness) and Rz (average maximum height) helps in assessing the suitability of the substrate for different coating applications.
Accurate measurement of surface roughness not only ensures stronger adhesion but also influences the longevity and performance of the applied coating. Inadequate surface preparation can lead to premature failure, peeling, or delamination, resulting in costly repairs and maintenance. Regular monitoring and assessment of surface roughness as part of quality control processes can optimise coating performance. Tools designed for various substrate materials and profiles provide flexibility in achieving desired surface characteristics, making them invaluable assets in industrial settings.
Environmental Considerations
Industries are increasingly aware of the environmental impact of their operations. Surface preparation techniques often involve chemicals and practices that can adversely affect air and water quality. Regulatory frameworks require businesses to adopt sustainable practices, pushing for the reduction of harmful emissions and wastewater. As a result, companies are now seeking alternative methods that minimise their ecological footprint while maintaining efficiency in surface preparation processes.
The adoption of eco-friendly surface preparation practices has gained momentum in various sectors. Many organisations are opting for methods that use biodegradable chemicals or water-based solutions instead of traditional solvents. These alternatives not only reduce toxic residue but also improve worker safety. Furthermore, techniques such as abrasive blasting using recycled materials are being embraced, contributing to waste reduction and promoting circular economy principles. Emphasising sustainability helps businesses meet compliance standards and enhances their reputation among environmentally conscious consumers.
Eco-Friendly Surface Preparation Practices
Environmental concerns are prompting the industrial sector to shift towards sustainable surface preparation methods. Techniques such as dry ice blasting and baking soda blasting utilise non-toxic materials that do not contribute to air or water pollution. These methods effectively remove contaminants without generating harmful waste, aligning with global efforts to reduce the carbon footprint of manufacturing processes.
Additionally, the adoption of biodegradable cleaning agents enhances eco-friendliness. These alternatives break down naturally and significantly lessen the environmental impact compared to traditional chemical solvents. Implementing water recycling systems can further minimise water usage and prevent contaminant discharge. Such innovations highlight the industry’s commitment to responsible practices while maintaining effective surface preparation techniques.
FAQS
What are the main industrial surface preparation techniques?
The main industrial surface preparation techniques include waterjet cutting, abrasive blasting, chemical cleaning, and various surface profiling methods.
How does waterjet cutting benefit surface preparation?
Waterjet cutting uses high-pressure water to effectively remove contaminants without damaging the underlying material, making it an efficient and precise method for surface preparation.
Why is measuring surface roughness important for coating adhesion?
Measuring surface roughness is crucial because it helps determine whether the surface is adequately prepared for coatings. Proper roughness enhances adhesion, ensuring that the coating performs well and lasts longer.
What eco-friendly practices can be used in surface preparation?
Eco-friendly practices in surface preparation include using biodegradable cleaning agents, minimising water and chemical usage, and employing techniques like dry ice blasting or waterjet cutting that produce less waste.
How can I ensure I am following environmental considerations in surface preparation?
To ensure compliance with environmental considerations, you should assess the materials and methods you use, opt for sustainable practices, and stay informed about regulations and industry standards related to surface preparation.
Related Links
Cost-Effective Industrial Painting Solutions for Brisbane's EnterprisesEnhancing Durability: The Role of Industrial Painters in Brisbane
Innovations in Industrial Coatings for Brisbane's Heavy Industry
The Impact of Weather on Industrial Painting Projects in Brisbane
Industrial Painters: Key Factors Influencing Paint Selection for Factories